What is a Wiring Harness? A Comprehensive Guide
Share Article:
Wiring harnesses are essential to the function of complex electrical systems. These organized assemblies of wires, connectors, and terminals are designed to route electrical power and signals efficiently throughout a system. By bundling cables into a single structure, a wiring harness simplifies installation, improves safety, and supports long-term reliability.
What is a Wiring Harness and What Does It Do?
A wiring harness is a structured grouping of wires, terminals, and connectors that transmits electrical power and data signals within a device or system. Rather than running individual wires separately, a harness organizes them into a single, compact unit that can be installed quickly and routed efficiently through tight or complex spaces.
The primary function of a wiring harness is to connect different components of an electrical system while protecting the wires from abrasion, vibration, and environmental exposure. Harnesses are often enclosed in protective sleeving, insulation, or tubing, which helps reduce wear and extend service life in demanding applications.
Types of Wiring Harnesses
Wiring harnesses are customized to meet the electrical, mechanical, and environmental requirements of their intended application. While the core function remains the same, the design and configuration can vary significantly depending on the use case.
Engine Harnesses: Commonly used in vehicles and equipment, engine harnesses are built to withstand heat, vibration, and chemical exposure while delivering reliable power and sensor connectivity to engine components.
Dashboard Harnesses: These assemblies connect various controls, displays, and electrical features within a vehicle’s dashboard. They’re often more compact and flexible to accommodate limited space.
Battery Cable Harnesses: Designed to carry high-current loads, battery harnesses feature heavy-gauge wires and reinforced insulation to ensure safe energy transfer.
Sensor Harnesses: These are used to connect input and output sensors in systems requiring precise data monitoring, such as medical devices or automation equipment.
Custom Wire Harnesses: Many harnesses are built to meet specific customer needs, whether for agricultural machinery, off-road vehicles, or industrial control panels.
What Materials Are Used in Wiring Harnesses?
The materials used in a wiring harness are selected based on performance, safety, and environmental demands. Each component contributes to electrical reliability, mechanical strength, and long-term durability.
Conductors: Most harnesses use copper wire for its excellent electrical conductivity and flexibility. In some cases, aluminum may be used for weight-sensitive applications.
Insulation: Wire insulation protects conductors from moisture, chemicals, and abrasion. Common materials include PVC, Teflon, and cross-linked polyethylene (XLPE), chosen for their resistance to heat and environmental stress.
Connectors and Terminals: These components form the interfaces between the harness and other devices or systems. They are typically made from plated metals like brass or tin for conductivity and corrosion resistance.
Protective Sleeving and Looms: Outer coverings such as braided sleeving, conduit, or heat shrink tubing help guard the harness from physical wear, vibration, and exposure to elements.
Tapes, Labels, and Fasteners: These accessories keep the harness organized during installation and allow for clear identification in servicing or troubleshooting.
Material choices depend on the application’s electrical load, environmental exposure, and compliance requirements.
Common Applications for Wiring Harnesses
Wiring harnesses are used in a wide range of industries to support complex electrical systems, especially where space, durability, and organization are key. Their versatility allows them to be adapted for both high-performance environments and everyday products.
Automotive and Transportation: Harnesses power lighting, sensors, infotainment, and control systems in cars, trucks, buses, and powersports vehicles. They help streamline wiring across tight spaces and vibration-prone environments.
Industrial Equipment: Used in robotics, machinery, and automation systems, harnesses support control panels, power distribution, and communication between components on the factory floor.
Medical Devices: In applications like imaging systems, diagnostic tools, and patient monitors, wiring harnesses offer compact, reliable connectivity in equipment that demands consistent performance and clean design.
Power Generation and Energy Systems: Harnesses manage power routing and monitoring in generators, solar equipment, and backup systems where rugged, high-load connections are critical.
Agricultural and Off-Road Equipment: Designed to withstand exposure to dirt, moisture, and extreme temperatures, these harnesses are built into tractors, harvesters, and utility vehicles.
Benefits of Wiring Harnesses
Wiring harnesses offer a range of functional and logistical advantages that make them essential in modern manufacturing.
Improved Organization: Bundling wires into a single harness reduces clutter and simplifies routing through equipment or enclosures.
Faster Installation: Pre-configured harnesses save time during assembly, reducing labor costs and the potential for wiring errors.
Enhanced Safety: Protective insulation and sleeving reduce the risk of short circuits, electrical fires, and damage caused by abrasion or vibration.
Reliable Performance: By securing wires in place and maintaining consistent connections, harnesses support stable electrical output in dynamic or harsh environments.
Space Efficiency: Compact design and customized layouts allow harnesses to fit into tight or irregular spaces without compromising function.
Explore Wiring Harness
Solutions at Kato Cable
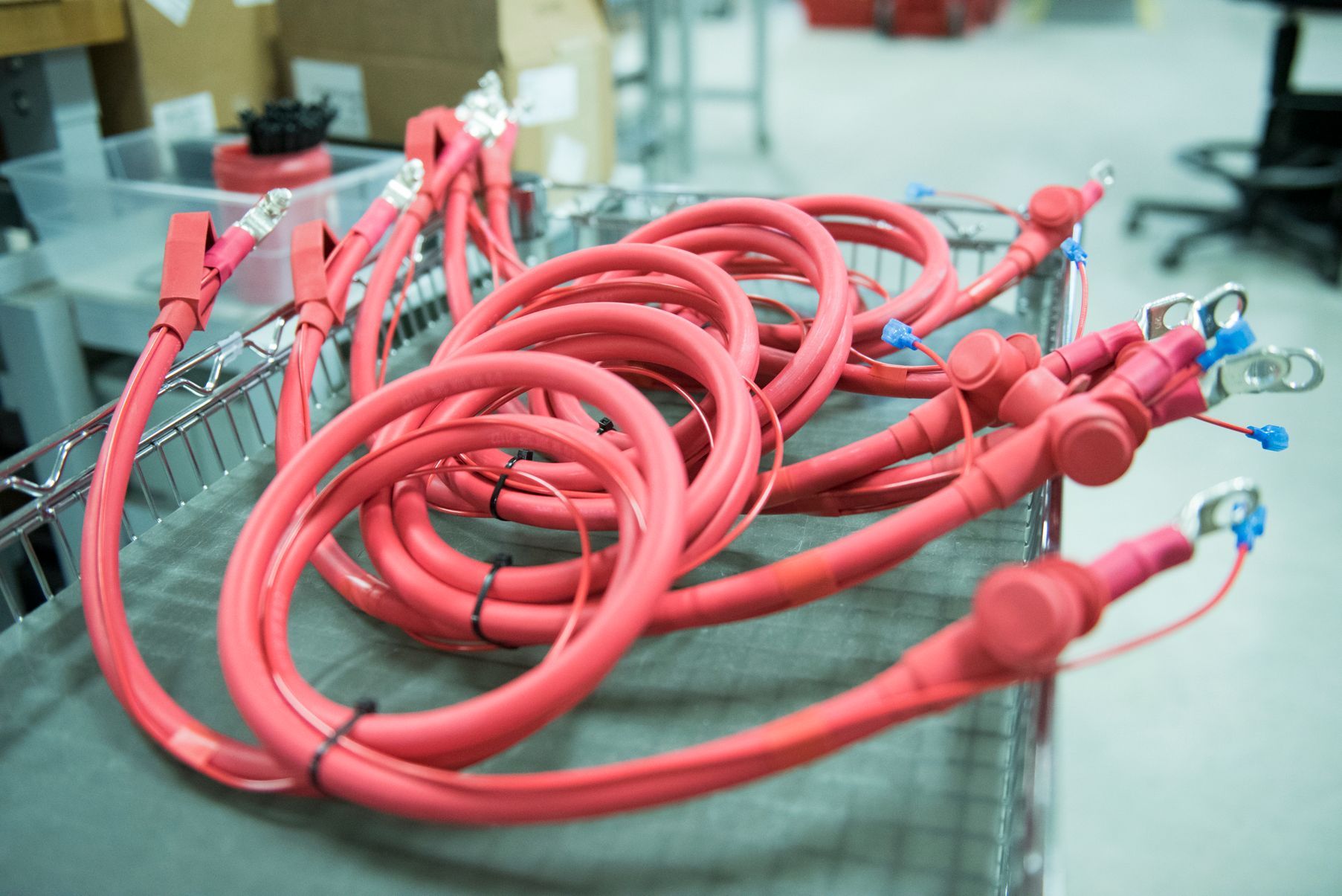
Kato Cable designs and manufactures wire harness assemblies for OEMs in the automotive, industrial, medical, power generation, and off-road equipment markets. Our team collaborates with customers to build solutions tailored to their electrical and environmental requirements.
With advanced wire processing capabilities and a strong focus on quality, we support programs from early-stage development through full-scale production. Whether you need high-volume output or a specialized configuration, Kato Cable delivers harnesses built for performance and reliability.
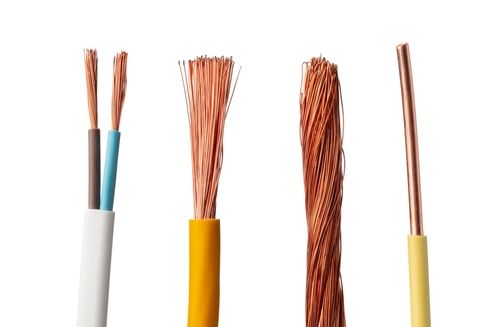